Quick links to articles in this edition
- Lightship declarations and the law
- New surveyor accreditation guidance manual part 2 now available
- Ensuring compliance of fixed fire systems on transitional vessels: type approval vs service certificates
- Electrical issues able to be identified by non-electrical periodic surveyors
- Timber boat surveying – with a focus on inspection of metallic fasteners
- Upcoming peak period for accreditation renewals
- New builds – duties of builders, designers and surveyors Survey matters suggestions
- Survey Matters suggestions
Lightship Declarations and the Law
The rationale underpinning the use of lightship declarations in SAGM Section 4.9, for Class 1 vessels less than 12m as well as Class 2, 3 and 4 vessels, has been raised several times in recent years. It has been argued that all vessels should perform a lightship check at 5-year intervals. While this may be attractive on a purely technical level there are other considerations at play.
While a lightship declaration might not have the same level of technical rigour as a lightship check, the latter was conservatively estimated to have a circa $50M impact on the DCV fleet collectively. This is a cost that was not previously imposed. An increase in the order of tens of millions would be exceptionally hard to justify without substantive incident data - particularly for vessels not previously subject to such an impost.
The requirement to perform a lightship survey has existed in the USL code since the early 1980’s. USL Code Section 8A Annex A Section A.5 required Class 1 vessels to perform a lightweight survey at an interval not exceeding 5 years, though in practice this was rarely enacted. Such a requirement did not exist for Class 2 & 3 vessels at the time.
During the development of NSAMS/SAGM, a decision was made to permit declarations for small Class 1 vessels as well as Class 2 and 3 vessels. At first glance, this might appear to be inconsistent, but the reality is that such a risk-based approach is more onerous than that of comparable jurisdictions worldwide, or in Australia previously under the USL Code.
The declaration is an important process to assist private marine surveyors to identify changes to a vessel which they may not have previously surveyed. Other countries (or class societies for that matter) do not require any periodic lightship declaration or measurement for non-passenger vessels.
Vessels undergoing modification are now captured in the transitional vessel process in Marine Order 503, which acts to prevent the stability related incidents of the past. Modifications that affect stability require that a lightship check be performed, and stability information updated as required. This is one of the primary reasons that lightship declarations are not accepted in alternate survey approvals when existing vessels undergo initial survey under Marine Order 503 Section 9.
Class 2 and 3 DCV’s that have perished in the past are often cited as reasons for conducting a full lightship check in lieu of a declaration. In most cases these vessels had undergone a significant change and would likely have transitioned under the current arrangements of Marine Order 503 and had their stability re-assessed.
As an example, the Canadian fishing vessel Tyhawk perished in 2021. The Tyhawk had added an additional deck (see figure 1 below). Were it a DCV, the addition of a deck is a change listed in item 7 (c) of Schedule 1 of Marine Order 503 and, under Section 9 (1)(c), would have required that the vessel undergo full initial survey including a lightship check and reassessment of stability.
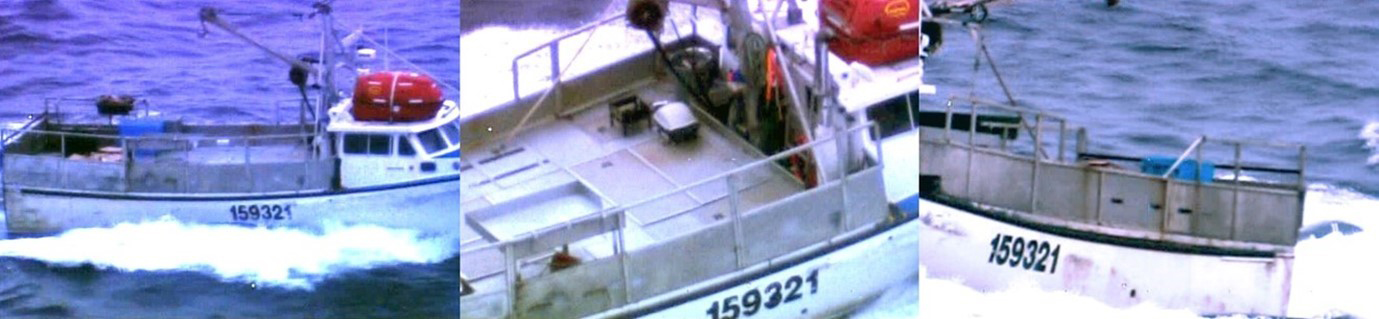
Figure 1 Tyhawk following modification, deck added show in bare aluminium. Source: Transportation Safety Board of Canada, Marine transportation safety investigation report M21A0065.
AMSA requests that accredited surveyors explain the importance of the lightship declaration to an owner. A person, such as the owner or master of a vessel, might commit an offence under section 137.1 of the Criminal Code Act 1995 if the person gives information to AMSA knowing that the information is false or misleading, or omits any detail without which the information is misleading.1
The message is that failing to declare pertinent changes (thus omitting to perform an act) is a serious offence. If the vessel were to later face a situation where a loss of stability leads to an incident, the connection between the false declaration and the incident would not be difficult to prove.
If the Owner or Master cannot be sure of any changes made to the vessel since the last inclining or practical stability test, or since the last Certificate of Survey was issued, they should engage the services of a competent person, such as a naval architect or an accredited surveyor. A lightship check and re-assessment of the stability against the relevant stability criteria may be subsequently required under SAGM 4.9.
The message to Owners or Masters in this case is, if you don’t know, don’t sign. To assist the AMS community in conveying this message, the AMSA 752 form will be altered to emphasise the legal importance of the declaration.
In summary, this is a risk-based solution. To require a lightship check at each renewal survey for every vessel would come at enormous expense to the industry and would vastly exceed standards applicable to the domestic fleet globally. The declaration system under SAGM 4.9 (6) serves as an additional safety benefit and correctly highlights the duties that apply to owners of domestic vessels to inform surveyors and the national regulator when making changes that affect vessel stability.
New Surveyor Accreditation Guidance Manual Part 2 now available
We have released the updated Surveyor Accreditation Guidance Manual Part 2 (SAGM) which comes into effect on 1 Jan 2025 and updated survey forms.
This manual outlines the standards and criteria required for the survey of domestic commercial vessels by Accredited Marine Surveyors and recognised organisations.
SAGM includes detailed technical, safety, and operational benchmarks established by AMSA, guiding surveyors in maintaining high standards of vessel safety and compliance.
- Increased owner control and flexibility with survey cycles.
- Owners of high survey frequency vessels can now choose to conduct their out-of-water survey in either year 2 or year 3 of the survey cycle.
- Owners of medium survey frequency vessels can choose to conduct their year 3 survey either in or out of the water.
- Simplified dual 2/4 class certification for leisure type vessels.
- Class 2 vessels engaged in leisure type activities (up to C waters) can now use the same CE certification for structural certification as Class 4 vessels, reducing regulatory burden for skippered Class 4 operations
- Clearer reporting obligations for repair and damage surveys.
- A definition has been added for "partial" surveys, along with a process described to allow reporting to AMSA.
- Use of own forms.
- The SAGM now allows any AMS to use their own survey reporting forms, provided these forms contain sufficient detail.
- Easier entry survey for restricted C class vessels.
- Design documentation requirements for restricted C class vessels have been made less burdensome.
- Significant detail added to the description of each survey type.
- A significant level of increased detail has been added to the descriptions of each survey type within Table 2 and Table 6.
Surveyors and organisations are encouraged to review the manual and to ensure familiarity before the changes come into effect on 1st Jan 2025.
Updated forms can be put into use immediately.
Ensuring Compliance of Fixed Fire Systems on Transitional Vessels: Type Approval vs Service certificates
Fixed fire systems on transitional vessels must meet the requirements of the NSCV C4 standard regardless of whether the USL Code applies to other fire safety items.
This article provides guidance on surveying fixed fire systems on transitional vessels, with a focus on the distinction between service certification and type approval, and there roles in confirming compliance with NSCV C4.
Understanding Transitional Vessels
Fixed fire systems are integral to the safety of commercial vessels. They are designed to suppress fires quickly and effectively, thereby reducing the risk of catastrophic damage or loss of life. For existing vessels, fixed fire systems are required to be maintained in good order in accordance with their original certification and service requirements. However, when a vessel transitions, existing systems must be examined to determine if they comply with the requirements of NSCV C4 - not just that they have been serviced.
NSCV C4 mandates that all fixed fire systems installed on commercial vessels must be designed, assessed, manufactured and installed in accordance with a standard mentioned in Table 14, where “assessed” is defined as:
Assessed: type assessed and verified as meeting the applicable standard or specification or test mentioned within this subsection, in a manner than complies with Chapter 18.
For a system to be accepted, each component, system or installation of active or passive fire protection measures must be tested and specifically listed for the purpose specified in NSCV C4 by
- Being tested and specifically listed as a fixed fire system by a NATA accredited laboratory, or a specialised laboratory such as the Scientific Service Laboratory (SSL);
- certified by a JAS-ANZ accredited product certification body;
- type approved by a recognised organisation; or
- certified by a Notified Body, recognised by the National Regulator, in accordance with the EU Marine Equipment Directive, Module B (MED-B).
- Evidence of this assessment is provided in the form of a type approval / listing certificate form the body that conducted the assessment.
A fire servicing agent or similar cannot provide this certification, they are not recognised as listing bodies by the NSCV.
Even if the fixed fire system has been in the vessel for a number of years, transition is a point in time where a surveyor is required to confirm that this system could be fitted to the vessel if it was now being built to contemporary standards.
Regardless of whether the system was previously accepted under a state scheme or previous standard, NSCV C4 requires that it has a current type approval / listing and could be accepted on a contemporary DCV today.
Service Certification vs. Type Approval: What’s the Difference?
Type assessment involves the certification of a product or component (in this case, a fixed fire system) by a recognized authority to confirm it meets the relevant standards. This process typically includes rigorous testing under controlled conditions to ensure the system’s effectiveness in a fire scenario. For transitional vessels, it is imperative to confirm that any installed fixed fire system holds a current type assessment with NSCV C4 specifications.
Service certification, on the other hand, is the ongoing verification that the installed system has been maintained. This includes regular maintenance checks, servicing, and testing, as well as compliance with installation standards. Service certification is crucial because even a type-assessed system can become ineffective if not correctly serviced and maintained, or if it has been modified without proper oversight.
Surveying Fixed Fire Systems on Transitional Vessels
Check Type Approval Documentation: Surveyors must request and review the type assessment documentation for the fixed fire system, which must clearly indicate that the system complies with the
relevant standards as outlined in NSCV C4.
This documentation can generally be obtained from the original equipment manufacturer.
What does this mean in practice?
In practice, this means that a system will need to be replaced if its type assessment certification has expired or been revoked - even if it has been in the vessel for several years.
AMSA is aware that there are several systems, previously acceptable under USL Code that do not have current listings and cannot be fitted onboard transitional or new DCV’s. This has occurred because:
- The system was listed / approved by a state marine safety agency and does not hold any national or internationally recognised listing.
- The listing for the system expired and has not been renewed by manufacturer. Expired listings/approvals are not valid.
- The extinguishing agent is environmentally damaging, and the manufacturer no longer maintains the approval.
If a fixed fire system on a transitional vessel does not hold current type assessment certification permitted under NSCV C4, it must be replaced with one that does.
Electrical issues able to be identified by non-electrical periodic surveyors
This topic raised at the recent Accredited Marine Surveyor Workshop generated considerable discussion:
Can a non-electrical accredited surveyor comment on potential electrical issues observed during a periodic survey?
An AMSA employee offered a helpful analogy: “Think of yourself as a GP. If you identify a potential issue, bring in the specialist—such as a licensed electrician or electrical surveyor.” This highlights that marine surveyors can and should note observations about electrical issues, even if they are not qualified to assess them fully.
There appears to be a misconception that surveyors cannot comment on electrical issues, which is incorrect. For instance if an electrical surveyor notices a cracked engine mount while inspecting generator mounts, they would be remiss not to include that observation in their report, even though don’t hold a machinery accreditation.
Similarly, if you observe clear examples of poor wiring, signs of overheating, damage to electrical enclosures, broken fittings or fixtures then these should be recorded as deficiencies requiring corrective action.
Following are examples of substandard wiring and electrical issues that would require rectification.
Unsecured and unprotected wiring and exposed conductive electrical components attached to an unsecured battery.
As above, an example of a very poorly installed electrical wiring installation
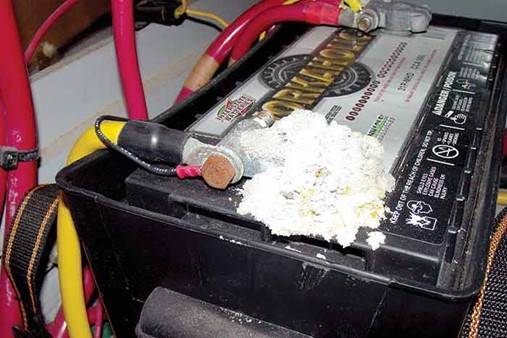
Poor battery maintenance. This white power is lead sulphate which is toxic to ingest and breathe. This can be prevented by keeping your battery dry and using a Dielectric grease on the terminals. Poor battery maintenance. This white power is lead sulphate which is toxic to ingest and breathe. This can be prevented by keeping your battery dry and using a Dielectric grease on the terminals.
AMSA is considering the development of an Instruction to Surveyors (ITS) to further assist the AMS be better equipped to identify and report these matters.
Timber boat surveying – with a focus on inspection of metallic fasteners
Surveying a timber boat is essential to ensure its safety, seaworthiness, and structural integrity. Timber boats, unlike those made of more modern materials like fiberglass or metal, require regular inspection and maintenance due to the natural properties of wood, which can be susceptible to issues such as rot, swelling, and pest damage. The main purposes of surveying a timber boat are to:
Identify structural weaknesses: Wood can deteriorate over time, so a survey helps identify issues such as rot, cracks, or damage from marine organisms. This is critical for the safety of the boat and its crew.
Evaluate repairs and maintenance needs: Regular surveys can pinpoint areas that need repair, maintenance, or replacement. This might include re-caulking seams, replacing damaged planks, or treating wood for pests.
Assess hull condition: The hull is especially vulnerable in timber boats. A survey can assess the condition of the hull, which is essential for water-tightness and overall buoyancy. Depending on the type of timber, the method of construction and the level of maintenance and protective coatings, timber boats take on or absorb water during their service life. This leads to increases in weight, rot or deterioration and can increase the likelihood of corrosion or damage to any metallic fasteners used in the construction of the vessel - especially for those vessels operating in salt water. Various metals are used are used in fasteners for timber vessel construction including galvanised mild steel, bronze, bronze alloys, stainless steel, and copper.
Ensure compliance with safety standards: AMSA requires commercial vessels including timber boats to undergo regular surveys to meet safety regulations. This is particularly important for boats used for passenger transport. By conducting a thorough survey, owners of timber boats can catch potential issues early, extend the life of the vessel, and ensure it remains safe and reliable on the water. Inspections should include:
- Internal Structure: Inspect frames, stringers, and other structural components, as well as any signs of rot, cracks, or separation.
- Deck and Cabin Inspection: Check for leaks, signs of water intrusion, and deteriorated joints in the deck, cabin, and other superstructures.
- Mechanical and Electrical Systems: Outline a basic inspection of these systems and their integration within a timber structure.
- Fasteners and Fittings: Examine metal fittings for corrosion and ensure bolts, screws, and other fasteners are intact.
Metallic fasteners and their modes of failure.
The failure of metallic fasteners in old timber boats is a common issue that can lead to significant structural deterioration and even compromise the safety and integrity of the vessel. The main causes and mechanisms behind this type of failure are outlined below.
Corrosion
Galvanic Corrosion: Different metals, when in contact with each other in a marine environment, can create an electrochemical reaction. For example, if iron fasteners are used alongside copper or bronze fittings, the iron can corrode quickly due to galvanic action.
Saltwater Exposure: Saltwater accelerates corrosion significantly. When metallic fasteners are exposed to seawater or even salt-laden air, they can corrode over time, weakening their ability to hold the timber planks together.
Crevice Corrosion: Areas where fasteners are embedded in the wood may trap water and other contaminants, creating an environment with limited oxygen that favours crevice corrosion. This localized attack can undermine the metal’s structural integrity from within and is a common failure with stainless steel fasteners.
Electrochemical reactions in wood
Acidity and Moisture in Wood: Wood itself contains organic acids and can absorb moisture from the surrounding environment, especially in bilge areas or hull regions below the waterline. These acidic conditions can lead to localized pitting or rusting of metallic fasteners, especially with iron or steel.
Galvanized Fastener Deterioration: In some cases, fasteners are galvanized or coated to resist corrosion. However, this coating can wear off over time, leaving the metal underneath exposed to further chemical degradation.
Mechanical stress and fatigue
Vibration and Load Cycles: The dynamic forces experienced by a boat, such as wave impact and load shifts, create repeated stress on the fasteners. Over decades, this can lead to metal fatigue, where micro-cracks develop in the fastener, eventually causing it to break.
Swelling and Shrinking of Wood: Wood naturally swells and shrinks due to changes in humidity and moisture. This movement places additional stress on the fasteners, causing wear and loosening over time.
Hidden deterioration
Embedment and Concealment: Many fasteners in timber boats are embedded within wooden joints or covered with plugs, making it challenging to inspect for signs of corrosion or wear. As a result, deterioration can remain unnoticed until it becomes severe.
Wood Rot and Structural Weakening: When rot sets into wood near metallic fasteners, it reduces the holding strength of the fastener in the timber and may lead to loosening or failure. Wood rot also creates an even more corrosive environment for metal components.
Preventive measures and remedies
Inspection and Replacement: Regular inspection of fasteners is crucial, especially in areas prone to high stress or saltwater exposure. For older boats, replacing corroded or fatigued fasteners with corrosion-resistant metals like silicon bronze or stainless steel can improve longevity.
Sealing and Isolation: Applying a protective sealant on metal fasteners or using non-metallic bushings can help isolate them from the wood and reduce galvanic reactions. Epoxy coatings or barrier paints on metal fasteners also help minimize corrosion.
Using Compatible Metals: When possible, using metals that are compatible with the surrounding materials can reduce galvanic corrosion. In many cases, using the same metal for all fasteners and fittings (like bronze) can prolong the structure's life.
Addressing these failure mechanisms early on is key to preserving the structural integrity of old timber boats and ensuring their continued use and safety.
Steps in surveying timber boats
Preliminary Inspection: Begin with an overview of the boat, looking for visible issues like:
Rust and Oxidation: Examine visible areas of fasteners for rust, which indicates potential corrosion.
Stainless steel or bronze fasteners should not rust in typical conditions, so any rusting indicates issues.
Loosening or Movement: Check if any fasteners are loose, as this could mean they have worn down or the wood around them has softened.
Discoloration in Wood: Dark staining around fasteners often indicates iron corrosion, which may signify weakening. Bronze can also leave green or blue stain, pointing to fastener degradation.
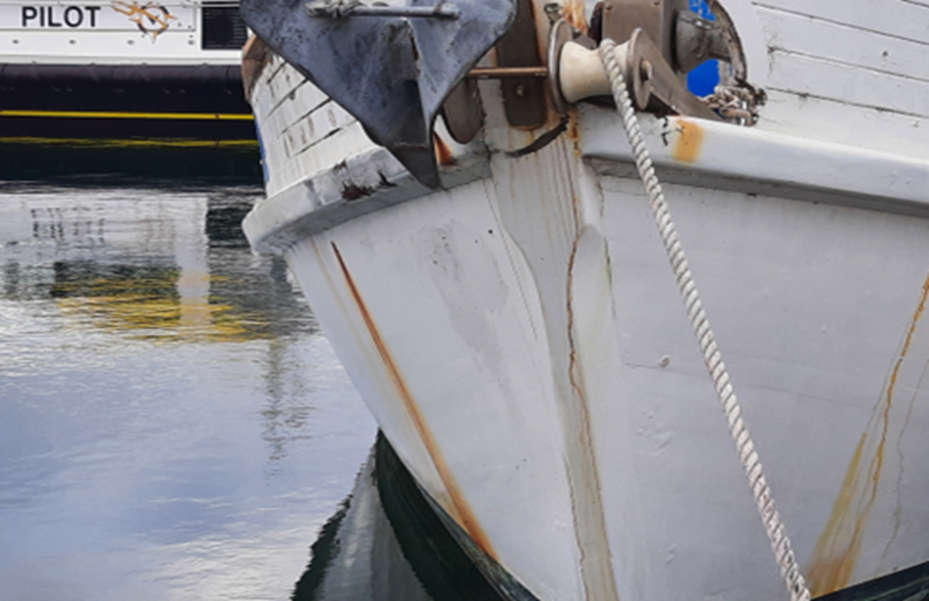
Rust streaks are often indicators of the type / material of fasteners and that corrosion or deterioration might require further inspection.
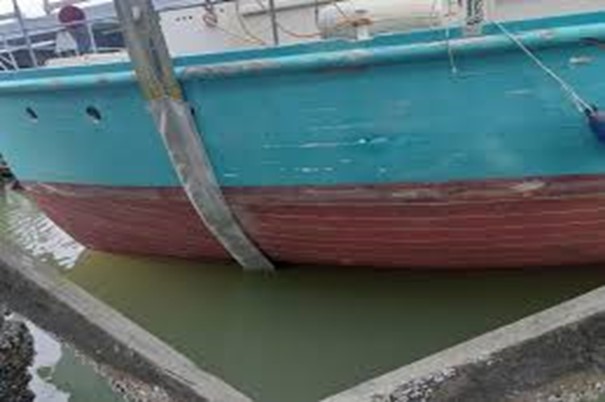
Inspection: Examine the hull below the waterline, checking for soft spots, seams, fasteners, and signs of rot.
Check caulked seams are consistently tight and compact. Use a sharpened awl to check for soft spots or rot in the timbers. Look for areas of blistered or raised paint that might indicate rot or swelling underneath. Consider removing selected pieces of copper sheathing (where fitted) to inspect / probe timbers underneath. Check major structural components around the shaft(s) and rudder post(s). Pay particular attention around hull penetrations - especially fresh water drains from galleys and bathrooms.
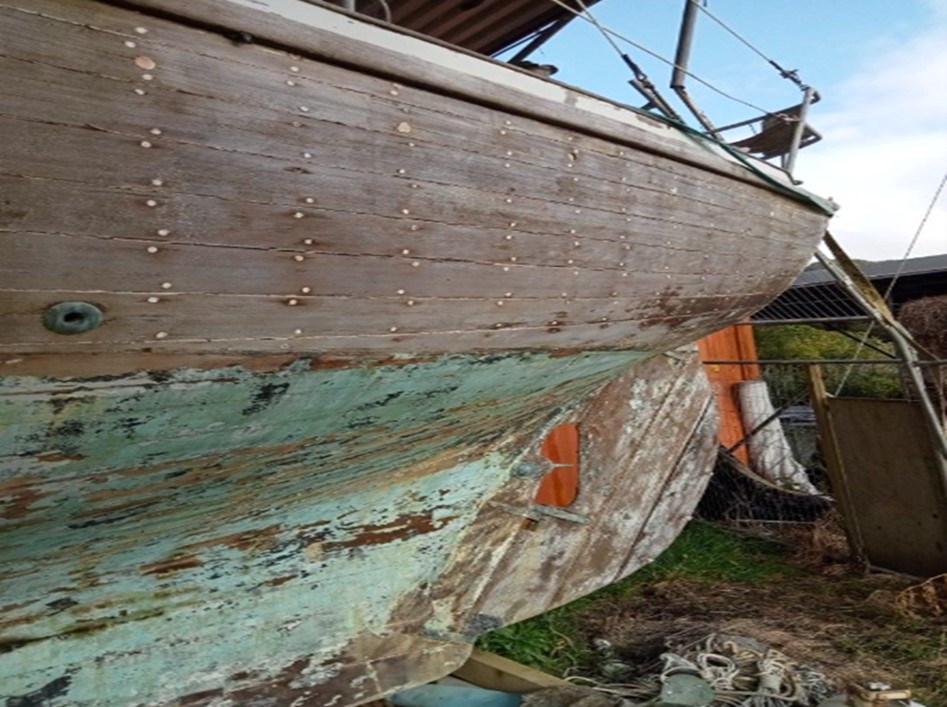
Once the underwater paint scheme has been stripped it may be easier to identify a random selection of fasteners for removal. These should include fasteners from the stem and stern post areas which will have been in place since the original construction of the vessel.
Non-destructive testing (NDT)
Ultrasonic Testing: Ultrasonic equipment can detect cracks or weak points in metal fasteners without removing them. This is particularly useful for inspecting fasteners embedded deep in the timber.
Magnetic Particle Inspection: This method can be used for ferrous fasteners to detect surface and slightly subsurface cracks.
Moisture Meters: Testing surrounding timber for moisture levels is essential, as wet wood accelerates corrosion and can rot around fasteners, causing loosening.
Removing sample fasteners
In some cases, removing a few fasteners for inspection can reveal hidden corrosion and deterioration patterns. This may be necessary if NDT is inconclusive or if the vessel shows signs of advanced corrosion.
SAGM Part 2 requires more in depth inspections at the 10 yearly or renewal survey interval and are reproduced below:
4.11 Scope and depth of a periodic or renewal survey
(1) A periodic or renewal survey must include the examinations, verifications, tests and trials of:
- the items specified in Table 9 relevant to the survey type unless otherwise approved in writing by the National Regulator; and
- as reasonably required by the surveyor in order to be satisfied that the vessel complies with the applicable legislation, exemptions and standards.
(2) In addition to the items specified in Table 9, the following inspections must be carried out on a vessel at every second renewal survey for the vessel, which should occur at intervals not exceeding 10 years and six months:
- ultrasonic thickness for vessels having metallic hull
- withdrawal of sample fastening for vessels having wooden hull
- hull in way of removable ballast
- verify internal foam buoyancy if not fully inspected during the five yearly in and out of water survey because of inaccessibility
- internal hull inspection if not fully inspected during the five yearly in and out of water survey because of inaccessibility;
- pressure test all sea water pipes
- internal fuel tank inspection of at least half the number of the tanks on board; and
- internal inspections of all other tanks not mentioned in Table 9.
Surveyors should use their observations of the hull and structure prior to the vessel being removed from the water to identify fasteners that are indicating signs of corrosion, wastage or failure. Depending on the fastener material, signs of corrosion or deterioration may not be clear or easy to identify. Surveyors should use their judgement and remove fasteners from high risk areas where fresh water, excessive moisture, poor ventilation, mould or rot are evident, or from areas where structural damage / previous repairs have been made for removal and inspection.
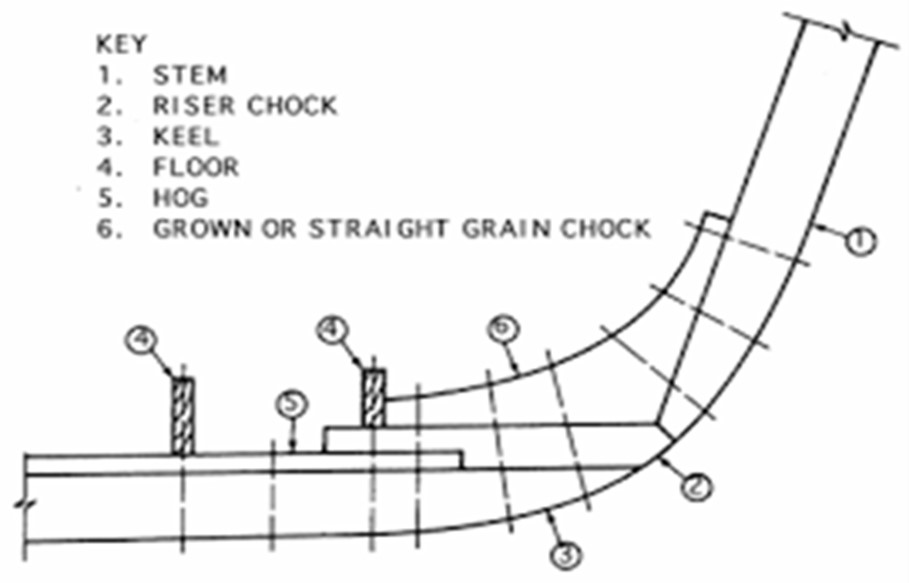
Typical keel to stem construction.
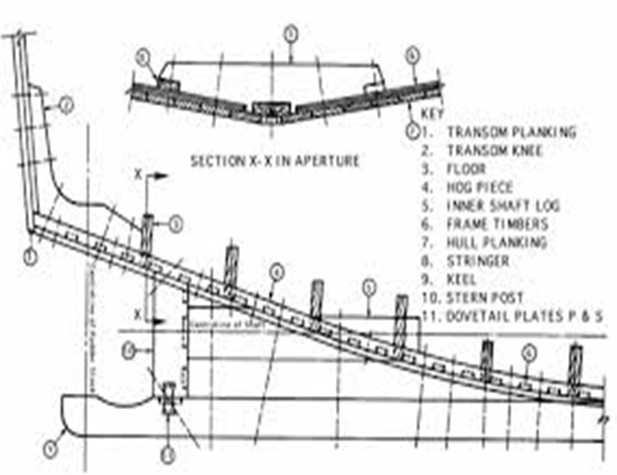
Typical keel to stern post construction.
Replacing corroded fasteners
Material Choice: Use corrosion-resistant materials like stainless steel or silicon bronze. Avoid mixing metals in close contact to reduce the risk of galvanic corrosion.
Protective Coatings: Consider using coatings or sealants around fasteners to minimize water ingress and slow corrosion.
Maintenance Best Practices: Offer tips on regular maintenance, such as sealing, painting, and antifouling treatments.
Protecting Against Moisture: Recommend preventative measures, including proper ventilation and regular cleaning.
Handling Repairs: Provide a basic guide on when to handle repairs and when to seek professional help, especially for issues like structural rot.
Conclusion
Routine inspections combined with preventative maintenance can help identify issues early and prolong the life of metallic fasteners in timber boats, preserving both safety and vessel longevity.
Upcoming peak period for Accreditation renewals
We have a large cohort of AMS who are coming up for accreditation renewal next year, to ensure applications are processed quickly please remember that a completed AMSA804 application must be received a minimum of three months before expiration of your accreditation.
What makes an AMSA804 application complete?
It must have:
- an updated photo for your new survey card,
- evidence of your professional membership including expiration date and
- evidence of continued professional development, either a statement and/or copies of certificates.
Be on the lookout for the reminder email. Toulla will send them out four months before your accreditation expiration date.
Float-free EPIRB maintenance: HRU and batteries
This is an important reminder to regularly review the hydrostatic release unit (HRU) and batteries on float-free Emergency Position Indicating Radio Beacons (EPIRBs) whilst undertaking surveys.
If a float-free EPIRB has been installed for 2 years or more, it’s time for owners and surveyors to give it the attention it deserves. Regular maintenance could make all the difference in an emergency.
Float-free EPIRBs are designed to automatically activate during emergencies. These water-activated distress EPIRBs are securely housed in a float-free bracket and deploy when a vessel capsizes at depths of 1–4 meters. Equipped with an HRU, the EPIRB floats to the water’s surface if unobstructed and immediately starts transmitting the distress signals.
For float-free EPIRB devices to work correctly, 2 critical components must be in top condition: the battery and the HRU. Batteries need regular checks due to their limited lifespan, and the HRU must be replaced every 2 years, unless the manufacturer specifies otherwise.
When conducting surveys, follow the manufacturer’s maintenance instructions, and inspect both battery and HRU as appropriate.
New builds – Duties of builders, designers and surveyors
General Safety Duties – Designers and builders
Designers and builders (amongst other persons) are required under Section 14 of the National Law to ensure that, as far as reasonably practicable, a vessel is safe if used for the purpose for which it was designed, commissioned and constructed. They shall carry out, or arrange the carrying out of such testing and examination as may be necessary to ensure the vessel is safe. A vessel that is found to be unsafe during builder trials which is subsequently allowed to enter service would be a breach of the general safety duties of the designer and builder.
Role of AMS in a new vessel build
Accredited Marine Surveyors (AMS) are tasked with assessing a vessel’s compliance with the applicable standards using the survey standards outlined in Marine Order 503 and the Marine Surveyors Accreditation Guidance Manual (SAGM). An AMS must not conduct a survey of a vessel while also acting in the capacity of an owner’s representative, as there may be a conflict of interest between the objectives of the owner and the AMS discharging their duties under the National Law. Similarly, the surveyor’s accreditation must not be used by the owner as a form of quality control over the builder to ensure that contractual requirements are met. This is usually the remit of the owner themselves, or an owner’s representative.
Vessel that is not fit for purpose
Criteria outlining a vessel’s fitness for purpose, and the metrics for establishing this, should be decided by the owner and builder and clearly outlined in the build contract. The owner may then wish to engage a competent third party as their representative to ensure that the builder fulfils their contractual obligations.
For example, a vessel meets all applicable standards and the initial surveys have been correctly completed, but its design is such that it does not meet the maximum laden speed specified in the contract. It is the remit of the designer and builder to ensure the problem is rectified – not the AMS, as it does not relate to safety.
Vessel that is unsafe
Section 6 of the National Law Act defines an unsafe vessel as one that is likely to endanger any persons for any reason. Clause 2.8 (5) of edition 3 of SAGM reinforces the requirement for a surveyor who identifies unsafe aspects of a vessel’s arrangement, construction, machinery, equipment or operational performance to report it to the National Regulator as soon as practicable. In addition, SAGM 3.11.2 outlines the various commissioning phase surveys and DCV-ITS-009 provides instructions for AMS undertaking these surveys.
The commissioning phase of initial survey should include vessel trials through which the propensity of a vessel to exhibit undesirable (unsafe) characteristics is checked. If the vessel is found to be unsafe during the course of a commissioning survey, the AMS must report the matter to AMSA, and work with the builder and/or designer to ensure such characteristics are rectified before recommending the survey.
For example, a DCV’s hullform and / or steering system performs dangerously whilst underway despite meeting the intact stability and engineering standards. Under the general safety duties, it is the remit of the persons responsible for the design, construction and testing of the vessel to ensure that these performance issues were identified and resolved. This ideally would be done by the builder prior to engaging an AMS to undertake the commissioning phase of initial survey. The commissioning AMS must not recommend the survey if the unsafe performance issues are not resolved.
AMS approving their own designs
It’s worth noting that an overlap exists between the general safety duties and accredited marine surveyors in instances where a person accredited in plan approval approves their own design and recommends it. In these instances, the general safety duties would also apply to them in their capacity as a designer. Acting as the plan approval surveyor does not relieve a designer of their general safety duties and as such, they must ensure the vessel is safe if used for the purpose for which it was designed. This should include witnessing the vessel performance during commissioning trials, ensuring design speeds and displacements are not exceeded, and verifying that the lightship particulars and associated stability criteria have been met for all loading conditions.
Conclusion
AMSA recommends that AMS undertaking the plan approval or commissioning phases of initial survey clearly establish with the builder and the designer the duties applicable to each party under National Law. Each party should agree on the criteria for acceptance of the commissioning trials as they relate to the detection and rectification of unsafe vessel matters not covered under the applicable technical or survey standards.
Survey Matters suggestions
AMSA wants to make sure Survey Matters is relevant and useful for accredited marine surveyors, boat builders, class societies, and others involved in the survey of domestic commercial vessels.
We encourage our readers to submit subject requests or ideas to DCVSurvey@amsa.gov.au for articles that would be of assistance to industry in future publications.
1 Updated on 12 February 2025: This sentence has been updated since its original publication.