Safety of Life at Sea Convention (SOLAS)
SOLAS requires the condition of the ship and its equipment is maintained to conform with the regulations to ensure that the ship remains fit to proceed to sea (SOLAS Chapter I, Reg 11).
SOLAS Chapter II-1, Reg 3-1 additionally requires that ships are maintained in compliance with the structural, mechanical, and electrical requirements of a classification society.
An effective maintenance management system will be the result of an assessment of the associated risks. When conducting the assessment, the operator should consider the following3.
- the maintenance recommendations and specifications of the equipment manufacturer
- the history of the equipment, including failures, defects and damage, and the corresponding remedial action
- the results of third-party inspections
- the age of the ship
- identified critical equipment or systems
- the consequences of the failure of the equipment on the safe operation of the ship.
International Safety Management (ISM) Code
Maintenance of the vessel and equipment is a requirement of the ISM Code (Clause 10.1). The ISM Code (Clause 10.2) also outlines that the Company/operator should ensure non-conformities are reported, and appropriate actions are taken. Non-conformity includes technical deficiency, which is a defect in, or failure in the operation of, a part of the vessel's structure or its machinery, equipment or fittings.
It is important that the operator rectifies the deficiency as soon as reasonably practicable, but also address the underlying maintenance management system failures (non-conformities) that led to the problem in the first place.
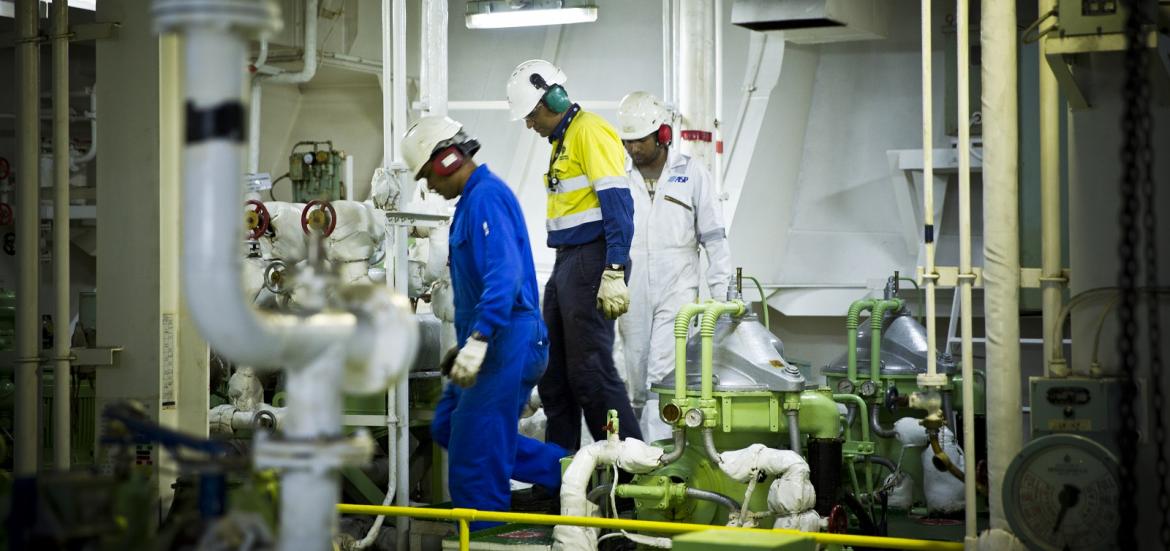
Importance of Planned Maintenance
Due to the complex nature of the maritime working environment, maintenance-related issues are often a result of interactions between organisational factors and latent conditions.
Fast turnaround times in ports3 put crew under immense pressure, leaving little or no time to complete critical checks and verifications. This can lead to gaps in maintenance due to time constraints.
Scarce resources mean crew and operators frequently have to make a trade-off between the time and effort taken to prepare for a task, and the time and effort expended doing it4. Trade-offs involving shortcuts may allow the ship to be operational more quickly, but at the expense of thoroughness and safety.
It is widely recognised that during the COVID-19 pandemic there have been difficulties ensuring effective maintenance of vessels. However, travel restrictions and quarantine requirements have largely been removed and any related issues are well known now for operators to plan for effective maintenance.
Poorly designed procedures that are unclear, out of date, inaccessible, not written for the task or are difficult to follow will likely result in deviation or non-compliance. It is important to align procedures with the way tasks are undertaken and to involve seafarers in their development whenever possible.
A well-designed planned maintenance system that includes regular and thorough maintenance, visual inspections and operational tests, will reduce the risk of machinery failure. Specific requirements and instructions, including any manufacturer’s recommendations should be incorporated in the testing and maintenance plans.
AMSA has recently published a Marine Notice 2022/10 Planned Maintenance on Ships5 emphasising the importance of planned maintenance in ensuring safe operation of ships and highlighting AMSA’s increased focus on planned maintenance during port State control inspections.
________________________________________________________________________________
Footnotes
1ATSB (2020) Grounding of Bulk India. Marine Occurrence Investigation 341-MO-2018-004
3 Allianz (2022) Safety and Shipping Review 2022.
4 Hollnagel, Erik (2009) The ETTO principle: efficiency-thoroughness trade-off—why things that go right sometimes go wrong. Risk Analysis, vol. 30,1, pp. 153-154.
5 AMSA (2022) Marine Notice 2022/10 Planned maintenance on ships.